Visit
prefabs website for more information

Are you curious about the timeline for constructing a modular home? The duration can vary, primarily influenced by the home's size and potential construction delays.
Building a modular or prefabricated home takes 16 to 31 weeks, including site preparation, post-construction details, and installing appliances and utilities. The process involves carefully coordinated steps, each contributing to your modular home's efficient and timely completion.
It's a fast and straightforward way to achieve your dream home without waiting.
How Long Do Modular Homes Take To Build?
Modular or prefabricated homes take 16 to 31 weeks to build, much faster than stick-built construction, which can span nine months to a year.
The construction process involves different steps, each taking a different amount of time. Here is the detailed process:
1. Architectural Design Phase (4–8 Weeks)
The first step in building your modular home is the design phase, which typically takes 4 to 8 weeks, depending on your house's size. During this exciting stage, you can choose everything from flooring to cabinets.
You will work closely with experts who advise and help customize your ideas. To ensure a smooth process, a site visit is scheduled. Designers will assess the property, including topology and amenities, and inquire about access routes. They will also determine site preparation time and approval requirements and create a budget. Once you agree on the design and budget, a 5% deposit kickstarts the construction of your new home.
2. Financial Planning Phase (1–5 Weeks)
Financing is a short but crucial phase in modular home building. Most modular companies offer financing, but if not, a homeowner mortgage works. Numerous funding options are available, with construction loans at a 5-8% recommended low interest rate.
This phase lasts one to five weeks, depending on the lender. Standard mortgages take a week, construction loans take eight to nine weeks, and modular firm financing gets approved in five to seven days.
3. Approval and Documentation Phase (4–10 Weeks)
This phase involves three key steps:
✔ Site Plan Approval: Once you receive the project drawings from your modular company, submit them to the local jurisdiction for review. This process may take several weeks for individuals but only about a week or two for a company's approval.
✔ Zoning Compliance: The city reviews your project to ensure it aligns with the necessary zoning regulations. If your project falls short, you can request a plan revision.
✔ Construction Permits: Accessing building permit approvals through the city website typically takes 2-4 weeks.
4. Building Preparation (2–3 Weeks)
Before building your modular home, all building details must align. City inspectors ensure plumbing and electrical connections meet standards. Company experts review and correct any overlooked details during the factory review phase, part of the construction process.
Measurements are meticulously checked to prevent errors, avoid material wastage, and ensure a watertight design before construction begins.
5. Factory Construction Phase (8–12 Weeks)
The duration of this phase depends on the house size. Factors like raw material availability, order volume, and the time of year can also affect construction time, though larger homes may take fewer weeks.
The builder constructs the home's exterior and interior framework in this phase. When leaving the factory, the house is already 85% complete. On-site work involves final touches like mud, electrical, and plumbing finishes.
6. Site Preparation Phase (1–4 Weeks)
Site preparation time varies based on factors like the access road, with buildings in remote areas possibly taking more time. The longest contractor time, usually two weeks, is for laying foundational bricks on uneven surfaces like hills.
Additional factors affecting this phase include:
✔ Access road construction
✔ Well construction
✔ Septic system
✔ Leach field
The overall duration depends on these elements and can be longer for more complex site conditions.
7. Foundation Establishment Phase (1–2 Weeks)
The foundation-laying timeline depends on house size and materials. For a raised basement, pouring concrete takes longer, and installing rebar for reinforcement is necessary beforehand.
If the foundation is not raised, pouring concrete may only take a few days. The type of backfill topsoil on-site determines whether hardened concrete is needed. Other foundation phase factors include plumbing, inspections, basement waterproofing, and backfilling. The process duration varies based on these considerations.
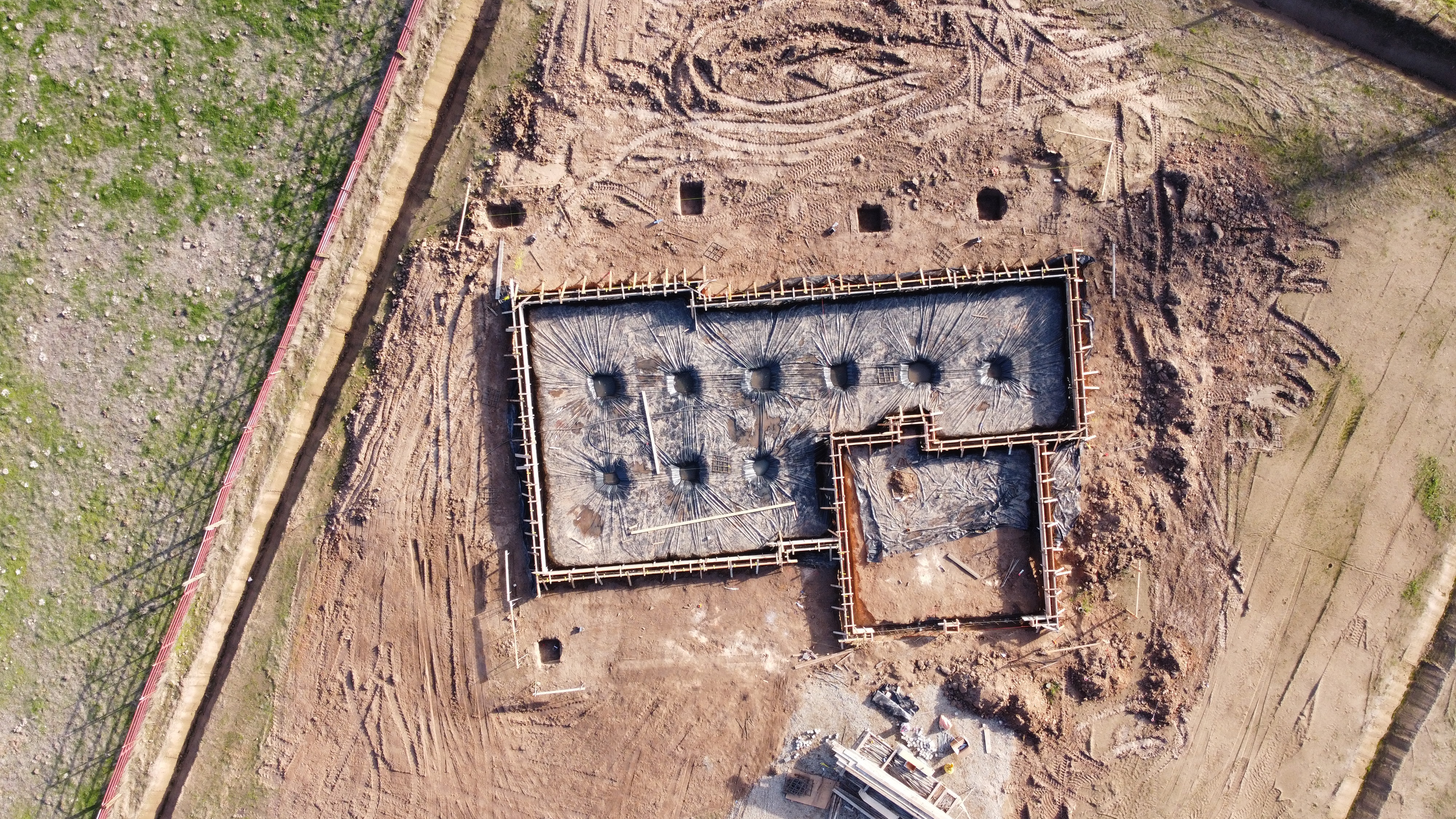
Time To Set Up A Modular Home
The actual on-site setup is generally quicker compared to traditional stick-built construction. Here is a general breakdown:
8. Framework Installation Phase (5–9 Weeks)
In this phase, the modular home is delivered to the site, and the installation process typically takes five to nine weeks.
Once the foundation is poured and cured, the house framework begins. Interior and exterior walls and the top-story floor are prefabricated and brought to the site. Within ten weeks, the framework is complete, and mud work starts. In the remaining weeks, the house is nearly finished.
9. Appliance Integration Phase (2–3 Days)
This stage involves the final touches and the completion of the electrical and plumbing work. Electrical appliances are connected and tested in all rooms, while plumbing is finished and tested. Taps, tubs, and the septic or sewer are checked for functionality.
The plumber ensures the house is airtight meeting city standards. All city inspection requirements are addressed, and the home undergoes a final inspection at this phase.
10. Site Finishing Phase (3–5 Weeks)
This phase involves installing fire escapes, creating lawns, and adding exterior elements like decks and swimming pools. Safety gadgets are installed, and the house design is reviewed to meet all agreed terms.
Appliances are tested before the final occupancy inspection is scheduled. The house is handed over to the owner once the company is satisfied with the work and the inspection is passed.
Check out the Interview with Plant Prefab Founder Steve Glenn, who shares prefab and modular construction insights.
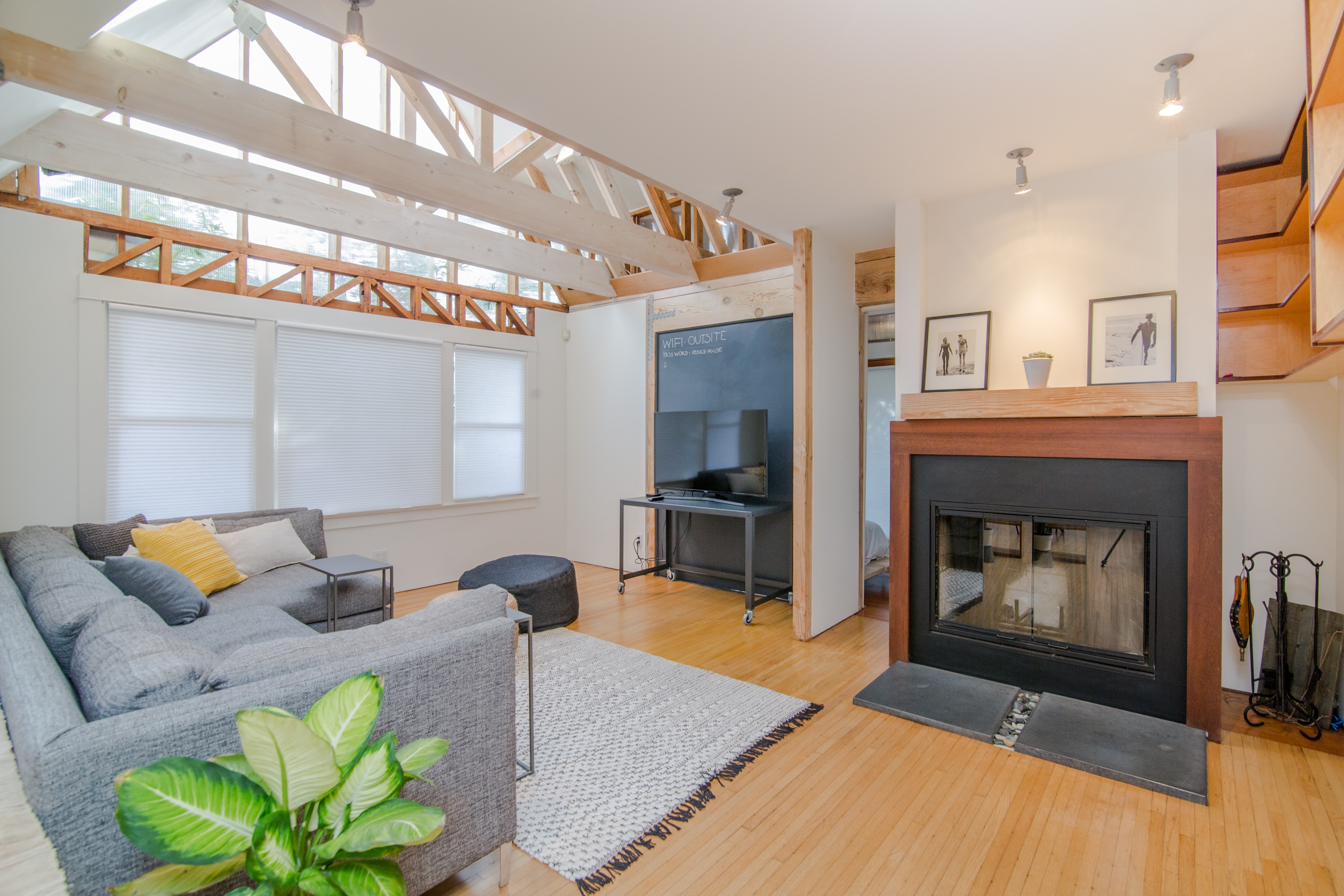
How Much Does A Modular Home Cost?
Modular home costs vary based on design and size. Smaller designs can cost around $80,000, while larger ones could reach $500,000.
Two key price points to consider are:
✔ Base Model Cost: Includes modular sections, delivery, and assembly.
✔ Finished Cost: Encompasses foundations, utilities, driveways, landscaping, decks, patios, permits, and other necessary expenses.
The finished cost is the most crucial, accounting for all essential elements. Base model costs range from $120,000-$150,000, but finished costs are around $270,000-$300,000, including extras.
Custom homes can significantly increase average prices, as customization adds to the base unit cost. While modular homes are generally cost-effective, extra features and customization drive up overall costs compared to standard housing.
The Land Cost
When planning a modular home, don't forget to factor in the land cost, which can be a significant part of the overall expense. Land prices vary by location, and construction is often the most expensive aspect.
For instance, in New Jersey, land can cost nearly $200,000 per acre, while Wyoming can offer better value at around $1,500 per acre. Northern Maine also provides options for affordable land.
Remember that within each state, the location, whether urban or rural, will affect land costs, with urban areas generally being more expensive.
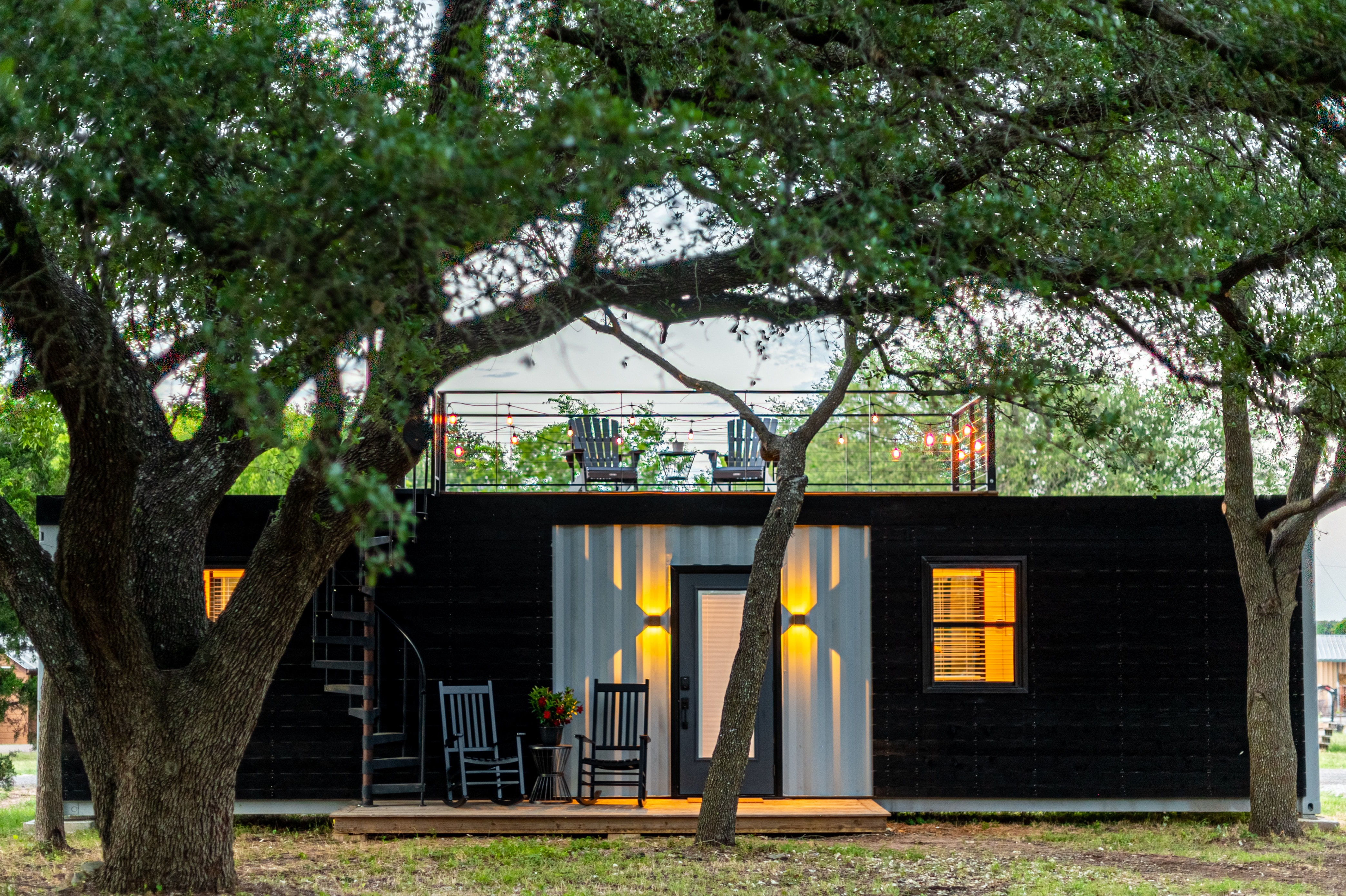
FAQs
How Fast Is Modular Construction?
Modular construction is way faster than Stick-built methods, with homes typically completed in 16 to 31 weeks. The efficiency comes from factory building, enabling simultaneous work on different components.
What Is The Lifespan Of A Modular Building?
Modular buildings fall into two main categories: temporary and permanent. It's noteworthy that permanent modular buildings can last for 35 years, 50 years, or even longer, depending on factors like construction quality and material resilience. Rigorous quality control measures and thoughtful foundation design make these structures long-lasting.